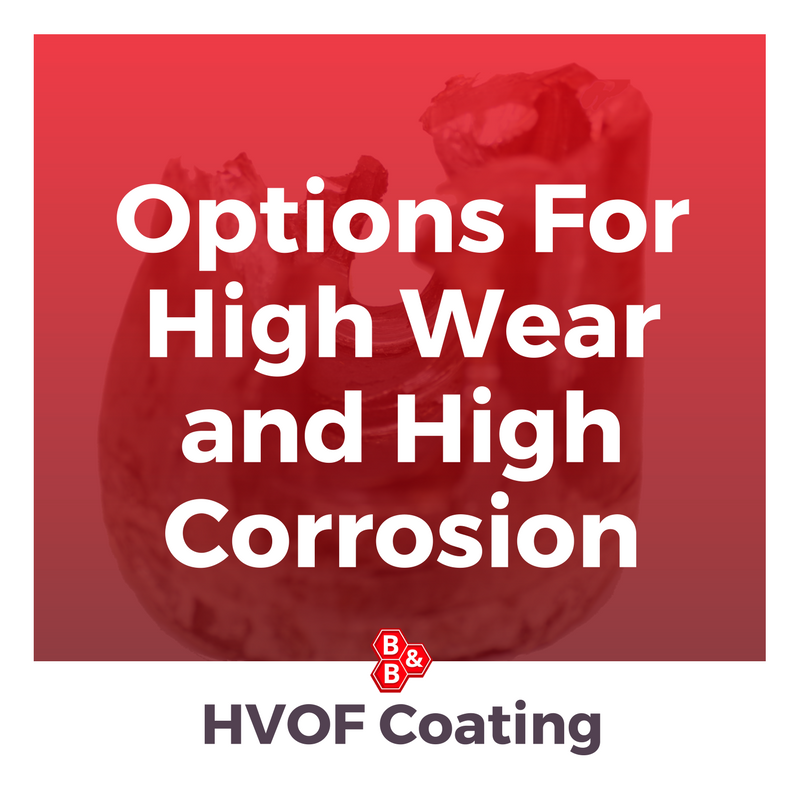
Across multiple industries, Wear and Corrosion represent a significant cost through the replacement of parts. There are a number of processes currently used to counteract these but few have the ideal qualities to withstand high levels of wear, corrosion, erosion and heat. Here is a breakdown of specific processes, and why they don’t currently meet industry needs.
Hard and Exotic Metals
One way in which industry has sought to counteract issues surrounding wear and corrosion has been to produce more parts from ‘Hard’ and ‘exotic’ metals. These include materials such as Inconel, Monel, Tungsten and Titanium. The issues with this are that these metals by their hard and dense nature of harder to machine and require more time and expert knowledge, which increases industry costs. It is also harder to source with both Titanium and Tungsten as both are placed on the Conflict Minerals list, again driving up costs. This is not a long term solution for the industry.
Hard Chrome Plating
Hard Chrome Plating is a very popular method of protection for components due to it’s ability to be built up into a thick, uniform coating that provides a higher level of hardness and corrosion protection. The issue with this as a process is the use of Hexavalent Chromium which is a known carcinogen. Not only does this make it unsafe to work with, but also bad for the environment due to the toxic waste and hydrogen gas produced. Hard Chrome as a process underwent heavy restrictions in September 2017. Any process that relies of Hexavalent Chromium is essentially a dead technology and so this is not a long term solution.
Hard Anodising
As a process Anodising is a conversion coating, this means that it forms both above and below the surface of the metal it is applied to, and will affect dimensional changes to the part. This makes it unsuitable for high precision parts for industries such as Aerospace and Oil and Gas. This is also a process which can only be used on aluminium components.
Electroless Nickel
Already a popular alternative to Hard Chrome and certainly more environmentally friendly, Electroless Nickel cracks at high temperatures and does not perform to the same degree when in corrosive environments as other processes.
Heat Treatment
This process is used in a wide variety of industries and although it will improve hardness and resistance to wear and high temperatures, it will not increase resistance to forms of corrosion. This process will extend part life, but cannot be used more than once without affecting dimensional changes to components, or becoming them too brittle.
Vacuum Coatings
Vacuum coatings are often used in small, high value items such as molds and dies. These coatings are extremely hard and offer excellent wear resistance, but this is a very expensive process and not suitable for mid to large sized components. m
So what’s the right solution?
B&B believe that HVOF applied coatings are the right solution for a wide variety of applications. This is because we can quickly formulate a specific coating to suit your need, using a wide variety of materials to give your component the desired attributes. These include materials such as Ceramics for electrical insulation, Tungsten Carbide for wear applications and Nickel Alloys for chemically corrosive environments. The process is much more environmentally friendly than others, and is cost effective when you consider the amount in which part life can be extended. The process is applied through a robotic arm and is suitable for a wide range of component sizes. We’re offering a free trial so that manufacturers can see for themselves the benefit of this process and compare. Get in touch today. B&B Coatings is based in Huddersfield, West Yorkshire and is fully ISO certified.
Comments are closed