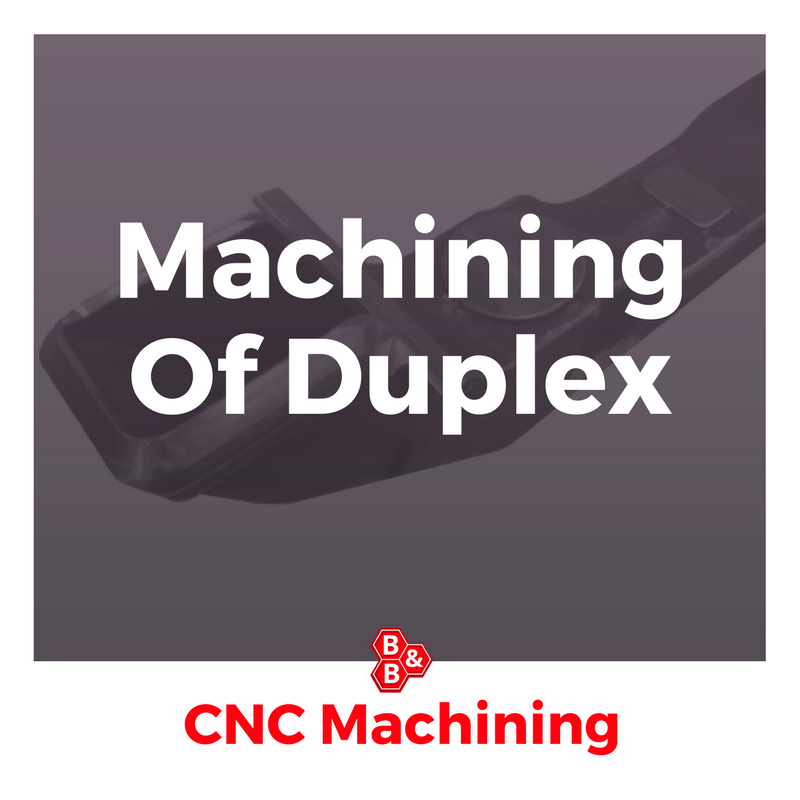
Duplex Stainless Steels are specified due to the high proof strength and resistance to corrosion (particularly Stress Corrosion Cracking) due to the lower Nickel content in their makeup, they are often cheaper than other grades with similar properties and their price more stable. The term ‘Duplex’ refers to the two-phase microstructure which incorporates both Ferrite and Austenite Grains.
Duplex Stainless Steels typically have about twice the strength when compared to their Austenitic counterparts, but this does not impact their machinability as much as you would imagine. Certainly you will need a stable setup and higher cutting forces and use of coolant are recommended. The main issue machinist may encounter when working with Duplex Stainless Steel is that the chip formed is strong and abrasive to tooling, especially the higher alloyed grades of Duplex. This means that you should expect rapid tool wear and a harder insert may be required for finer finishing.
Another factor in tool life is the work hardening that is much more pronounced in Austentitc and Duplex Stainless Steel that in their Carbon or Ferritic counterparts. In order to combat this its important design machining sequences that always provide a depth which will be below the work hardened layer from the previous pass and avoid dull geometries. A generous depth of cut is recommended.
Stainless Steels do have a tendency to stick to the tool, and this problem is especially profound where the cutting speed is too small. Try and use a machine that has a gearbox spindle that provides higher power at lower revs.
As a sub-contract machinist, B&B have the machines, experience and knowledge to manufacture a range of components out of Duplex Stainless Steels. Common applications include Gasket, Flanges and Pipelines used in oil and Gas Pipelines and Ocean Mining Machinery. B&B are an ISO certified company serving the whole UK and supplying high precision components to your specifications.
Comments are closed