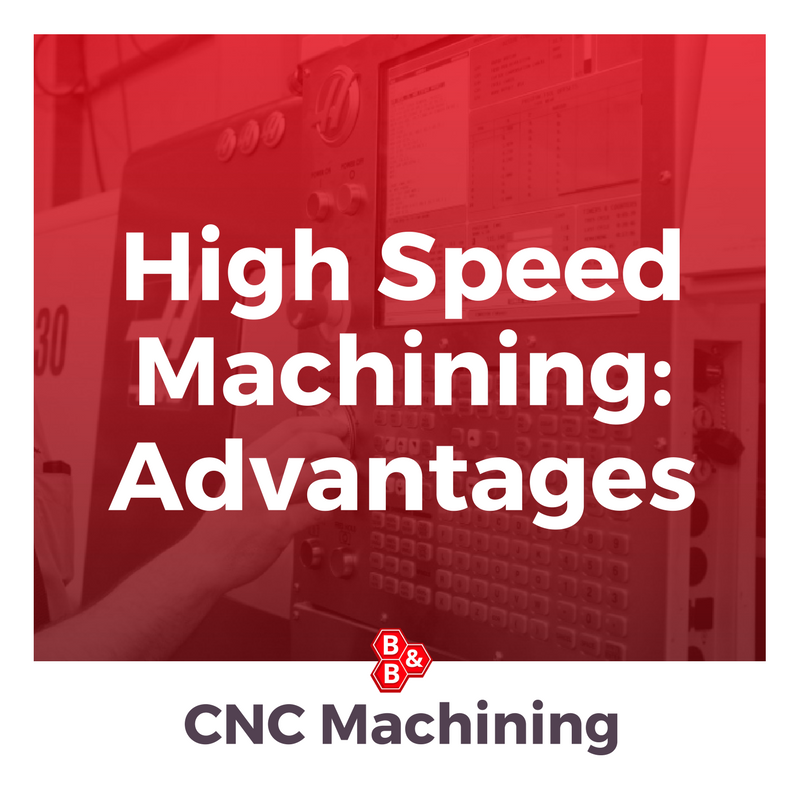
The idea of producing parts more quickly and therefore more cost effectively is appealing to many manufacturing companies, but the reality is that there is more to it than just a combination of the right tools and higher speeds.
How do you define it?
Some people define High Speed machining as high cutting feeds, or cutting speed or even a combination of the two. Some people will define it as spindle speeds running over a specified minimum rpm. Here at B&B precision we think of it in terms of productivity. What speeds can we achieve that will make our work more productive without sacrificing quality.
What are the advantages?
High speed machining allows us to achieve higher removal rates which in turn improves our productivity and lowers cost. This gives us a competitive edge and is one of the reasons why B&B are able to provide such competitive pricing.
At higher speeds, cutting forces are lower and less heat is generated which in turn means less risk of tool deflection or workpiece distortion. This is a crucial factor in any precision engineering, but is especially important when working on components with thin walls or made from harder metals.
At higher speeds chips are smaller and are evacuated more easily, even when machining dry.
In high speed machining, you can achieve surface finishes with low friction, often ad good as Ra~ 0.2um
At higher speeds, cuts are shallower and the engagement time for the cutting edge is extremely short. This allows for a productive cutting process of small sized components as well as finishing.
High speed machining is not without its risks and there are many factors including the machine, the cutting tool, the material being used and the operator which all come into play. As a sub-contract machinist B&B Precision are used to handling a wide range of components and materials. We can provide high speed machining for precision parts. We are fully ISO certified and based in Huddersfield, West Yorkshire.
Comments are closed