
Hard turning is not a grinding process but is a process that for the correct applications can be a better alternative to Cylindrical Grinding. B&B offers Hard Turning to customers alongside conventional grinding processes and so is able help you choose the best solution for you particular requirements.
Grinding advantages:
• Superior Surface Finish
• Higher Dimensional Roundness
Hard Turning advantages:
• Improved Concentricity
• Reduced manufacturing operations
• Reduced manufacturing operation cycle times
The “sweet spot” for hard turning applications are for components that have roundness accuracy requirements between 0.8 and 12 microns, and surface roughness requirements between Rz 0.8 micron and Rz 7.0 microns.
The process of hard turning shares many fundamentals with its “soft turning” sibling. Hard Part Turning gives has inherent advantages over grinding but requires specific knowledge and experience that not all machinists possess. As the capabilities of modern turning centers continue to increase so does the range of possible applications – please talk to us about your requirements and we can recommend the optimum solution.
Hard Turning is typically defined as the turning of a part harder than 45HRC on a CNC turning centre. Since surface roughness of Rmax/Rz=1.6s can be achieved, Hard Turning is often considered a replacement for Grinding operations or as a pre-grinding process. Hard Turning is most often performed on post-heat treated parts with surface hardness ranging from 45HRC to 68HRC or even higher.
Grinding has the advantage of being able to achieve higher dimensional roundness and cylindricity accuracy compared with Hard Turning. However, since parts can typically be finished in a single chucking, Hard Turned Parts often show superior concentricity and perpendicularity characteristics to their ground counterparts.
The cost advantages of Hard Turning compared with Grinding are numerous. Additionally, several types of Grinding machines may be needed to perform the operations able to be performed on a single Turning center.
A turning center can complete ID turning, OD turning, taper turning, and grooving in a single chucking. In addition to improving the accuracy of squareness, concentricity and straightness, this drastically reduces cycle and setup times as well. High precision threading operations can also be performed, guaranteeing concentricity with other part features compared with offline threading operations.
Hard Part Turning also allows for the finishing of radius and free-curved surfaces. Grinding processes require a custom-dressed wheel, which is time consuming to produce, or highly customised Grinding machines that can be expensive.
In addition to the inherent cost advantages of combining multiple operations into one, Hard Turning cycle times are drastically shorter than comparable grinding operations. Metal can be removed much faster in Hard Turning operations, and high speed Turning is possible with both CBN and ceramic cutting tools. Changing Grinding wheels is also time consuming, whereas switching out inserts on turning centers can be quick. Part loading and unloading times are also shorter for turning centers, and turning centers are typically more easily automated for additional productivity.
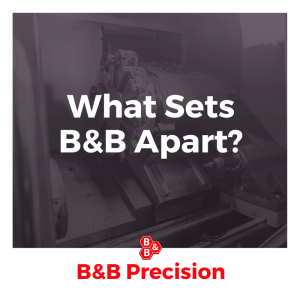

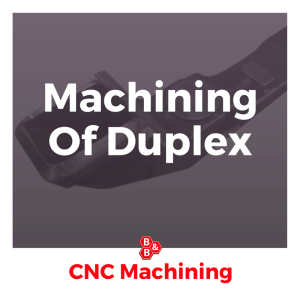
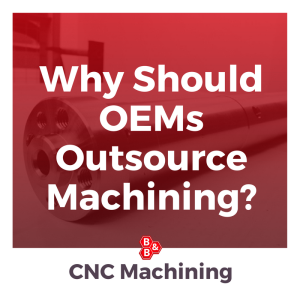
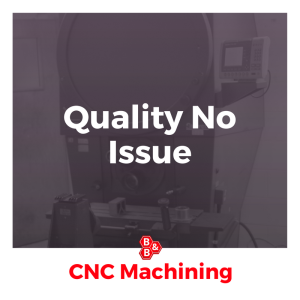
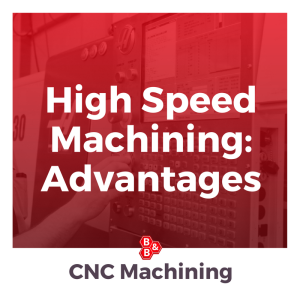
Company Registration Number: 03639121
VAT Number: 721236968
DUNS Number: 236438573
ISO Certificate: 8512-ISO 9001:2015