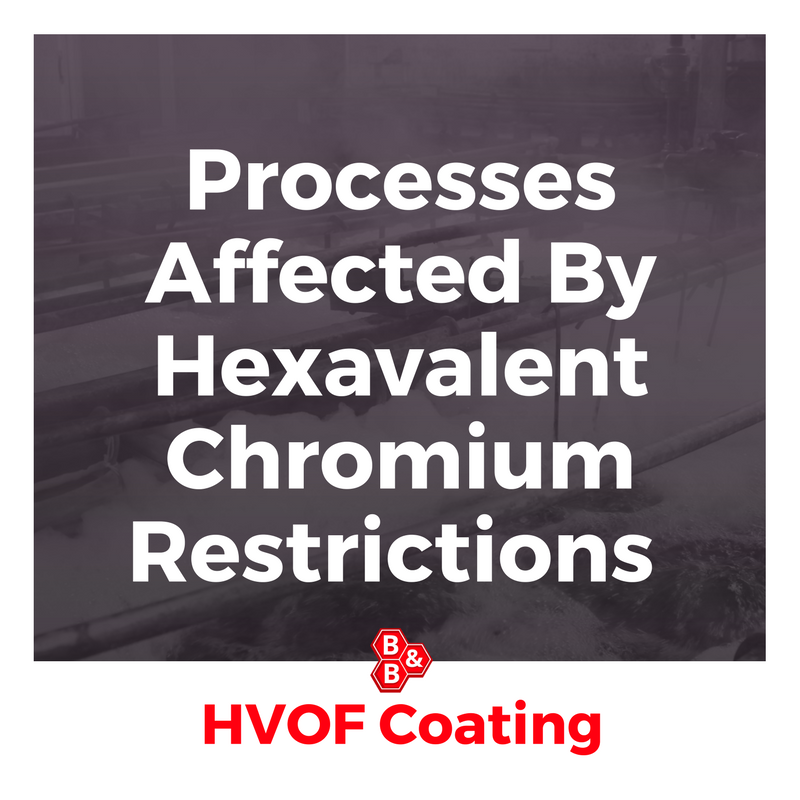
Hexavalent Chromium has long been on the ECHA’s list of annexed substances due to its carcinogenic nature. On the 21st of September 2017 further restrictions came into play and this means manufacturers across the country have had to look for an alternative. So what processes are affected and how are companies reacting?
Alocrom 1000 and 1200
Hexavalent Chrome is a key ingredient within Alocrom conversion coatings which are used to improve the corrosion resistance and act as an undercoat before painting on aluminium components. Manufacturers looking for environmentally friendly alternatives could try Iridite NCP or Surtec 650V which are both suitable for similar applications.
Zinc Plating
Zinc plating might not be the process which automatically springs to mind when we think of Hexavalent Chromium, but it is used as part of the passivation process which normally gives Zinc Plating enhanced corrosion resistance as well as contributing to its colour. In order to counteract this, Trivalent based solutions have been adapted that are able to perform to the same level. Trivalent Chromium does not produce the same hazardous by-products as Hexavalent Chrome. The only noticeable effect that this process will have is that it produces ‘weaker’ colours.
Chrome Plating
Would this mean that Chrome Plating utilising Trivalent Chromium is possible? The answer is yes and no. Trivalent Chrome Plating has been tried and developed but is not yet largely commercially available. As a process it is only suitable for coatings a few millionths of an inch thick, but that doesn’t mean it’s not possible. Decorative Chrome Plating is actually a layer of Nickel Plating with a chromium flash and so for these sorts of applications, Trivalent based Chromium may be an option. We would expect to see a commercial push for Decorative Chrome Plating using Trivalent Chrome in the near future.
Hard Chrome
The question is then, whether or not a Trivalent Hard Chrome Plating option is a viable alternative? When asked if Trivalent based Hard Chrome could replicate the results of the current process, Ted Mooney of Finishing.com says “My understanding is that it can’t because the process is still only suitable for coatings of a few millionths of an inch thick, not several thousandths.” This means that thick, dense coatings would not be possible with Trivalent Hard Chrome. This is a key factor in the corrosion and wear resistance properties of Hard Chrome to begin with and as such a suitable alternative is still needed.
Thermal Spray Processes
Many engineers will be familiar with the term ‘metal spraying’ and essentially Thermal Spray Processes are a modern version of that. They take material, heat it up and fire it out at a substrate. Thermal Spray Processes are hard and dense in nature and produce coatings with a high bond strength and low porosity. HVOF is one Thermal Spray Process which is especially suited to spray carbide materials which are able to outperform Hard Chrome on a number of fronts and depending on your application, can be specially configured with materials to suit.
Get in touch with B&B today, we can give you all the information you’ll need on the right materials for your application as well as giving you an overview on costs and turnaround. We provide HVOF applied coatings including Stellite 6, Tungsten Carbide, Ceramics and many more. We are ISO certified and based in Huddersfield, West Yorkshire. mail@bandbprecision.co.uk or call 01484866386
Comments are closed