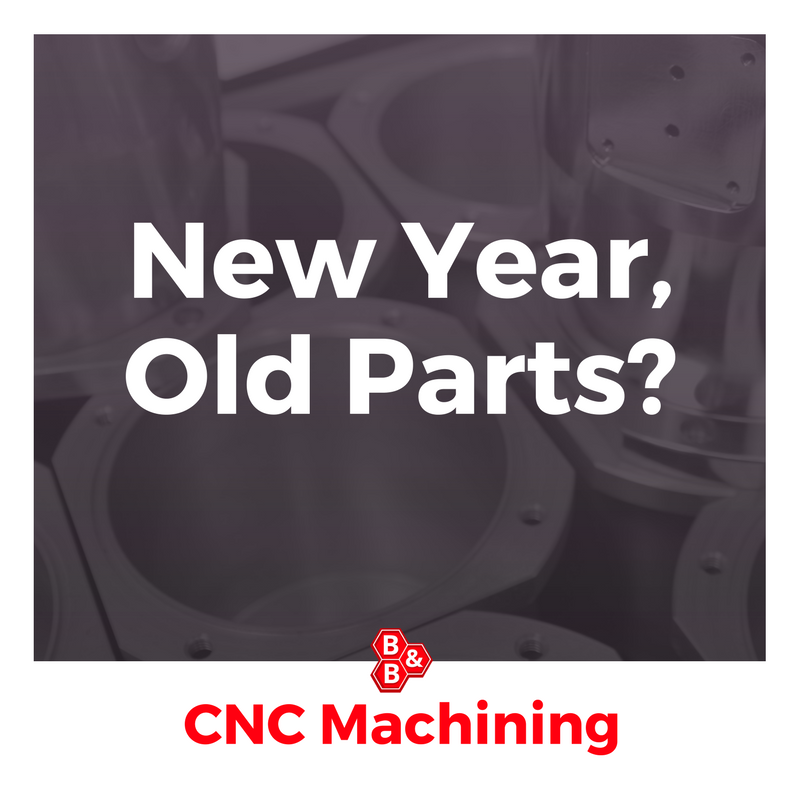
While many other businesses were winding down for Christmas most factories and foundries will have been squeezing every minute out of the day in order to fulfil the pre-holiday demand. This often puts extra stress and strain on legacy machinery and may result in failures. For many businesses, January represents a chance to start a fresh and conduct preventative maintenance, but what are your options when a part has come to the end of its life?
Buy New Equipment
Any machinery should be a long term investment for your business and no doubt you should have got many years of service out of your current machine. Where you start to have a large number of faults on your machine it can be tempting to replace it. Don’t underestimate the cost of breakdown to your business, not only in time and profit lost but of course in call out charges and new parts if available. If you are considering replacing a machine it’s important to first find the time to dissemble and inspect your components and evaluate whether it is the system at fault or a particular part/set of parts.
Replacement of Parts
Most machine manufacturers usually have an inventory for any given machine for around 20 years or so, so in theory it should be possible to find replacement parts. This can be a lot trickier where the original manufacturer is based abroad or has since stopped operating, or perhaps your particular model is now obsolete. In these scenarios it may actually be quicker and more cost effective to reverse engineer a new part from scratch.
Repair Existing Components
In some cases it may be possible to repair your original part at lower cost than replacement. One common source of failure is wear and in these cases it may be possible to weld/coat an item back to its original size and then grind so as its fit for purpose. These processes tend to be used on for large hydraulics, shafts, impellers and rotors. B&B will often build up a worn shaft back to its original size using thermal spray coatings and then grind for tolerance.
Create New Components
Where the original manufacturer may have ceased trading, and repair of the part is not possible it may be wiser to create a new part from scratch. Often using the broken component as a base to create a new 3D model, we identify the material used and then use our CNC machines to create a new component. We can also work alongside local casting and fabrication companies to supply complete.
Extending or replacing components for your machine is often less expensive than buying a new one and is especially prudent for any machinery that must work with acidic materials, high temperatures of high wear.
Comments are closed